Causes and Solutions of Cracking in Putty Powder - The Key Role of HPMC
Cracked putty reduces the effectiveness and appearance of the wall. This article clearly explains the causes of putty cracking, in particular the important influence of hydroxypropyl methylcellulose (HPMC), and practical solutions to avoid this problem.

1.What Causes Putty Powder to Crack?
Putty powder cracking is a common issue encountered during wall finishing. Several reasons can lead to cracking:
- Incorrect Proportion of Ingredients:
When materials like cement, calcium carbonate, or gypsum are not mixed in the proper ratio, putty cracks may occur.
- Poor Quality Raw Materials:
Low-quality materials or expired additives can weaken adhesion, causing cracks.
- Improper Application Techniques:
Incorrect thickness or uneven application can lead to drying stress and cracks.
- Environmental Conditions:
Drying too fast or excessive moisture during application can create cracks.

2.How Does HPMC Affect the Quality of Putty Powder?
Hydroxypropyl methylcellulose (HPMC) is an essential additive for putty powder. It significantly affects its performance in several ways:
- Water Retention:
HPMC improves water retention, slowing down drying speed, which helps prevent cracks from forming due to rapid drying.
- Adhesion and Flexibility:
HPMC enhances adhesion between the putty and the wall, reducing the risk of detachment and cracking.
- Workability Improvement:
With HPMC, the putty powder mixture becomes smoother and easier to apply, reducing unevenness and subsequent cracking.
- Stability:
Properly formulated HPMC maintains consistent quality and stability in storage and application, reducing defect rates.
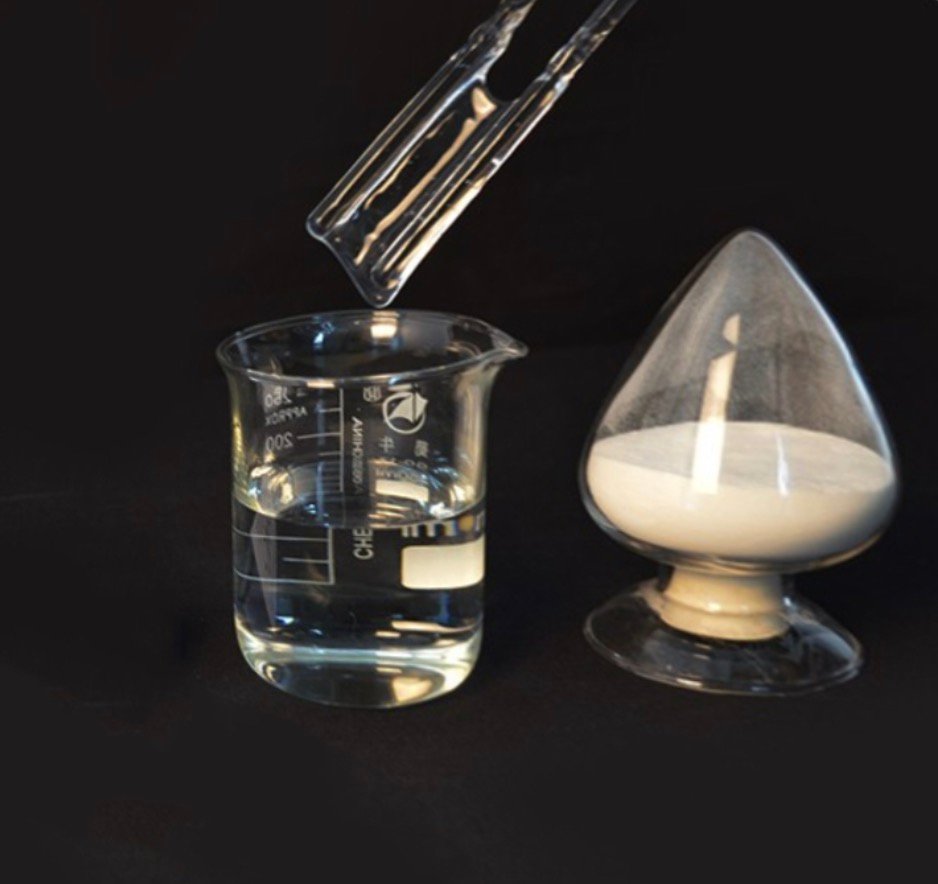
3.Adjusting HPMC to Prevent Cracks
To ensure the best results and avoid cracking, you can adjust the properties of HPMC as follows:
- Increase Viscosity Slightly:
A higher viscosity HPMC increases water retention, effectively reducing cracks. Adjust the viscosity level according to your product's specific needs.
- Optimize Dosage:
Typically, adding between 0.2% and 0.5% of HPMC by weight is ideal. Adjust according to the local climate and material formulation to prevent cracking effectively.
- Quality Selection:
Always use high-quality, consistent HPMC. Lower-grade materials may save costs initially but increase long-term risks of product failure.
- Test and Evaluate Regularly:
Perform small-scale tests whenever you change the HPMC type or dosage, and observe carefully to ensure no cracking occurs before mass production.
4.Practical Solutions to Avoid Cracking
Besides adjusting HPMC, implement the following practical guidelines:
- Correct Formulation:Ensure accurate ratios of all ingredients (calcium carbonate, cement, gypsum, etc.).
- Proper Mixing Technique:Mix thoroughly to achieve a smooth and even paste, eliminating lumps.
- Controlled Drying Environment:Maintain moderate humidity and temperature to reduce drying stress.
- Application Standards:Follow recommended layer thicknesses (typically 1-2 mm per layer) and avoid overly thick applications.
5.Ensuring Quality with Proper HPMC Use
Cracking in putty powder can be effectively prevented by understanding and managing the critical role of HPMC. Selecting high-quality HPMC, correctly adjusting dosage and viscosity, following precise formulation and application methods, and controlling environmental conditions will greatly improve your product’s quality, reduce customer complaints, and enhance overall satisfaction.
A professional understanding of how HPMC affects putty powder quality enables manufacturers and users to create reliable, high-quality products. Follow the guidelines outlined above to achieve consistent, crack-free results every time.